Dan,
With default precision and 45 mm stroke you must to be able to move your pot handle with step of 0.45 mm. If you need more precision, how can you control this by your hand?
See this video - with A0 assigned as default Throttle the RPM can be changed with precision about 20 rpm.
How did you get 300 prm step?
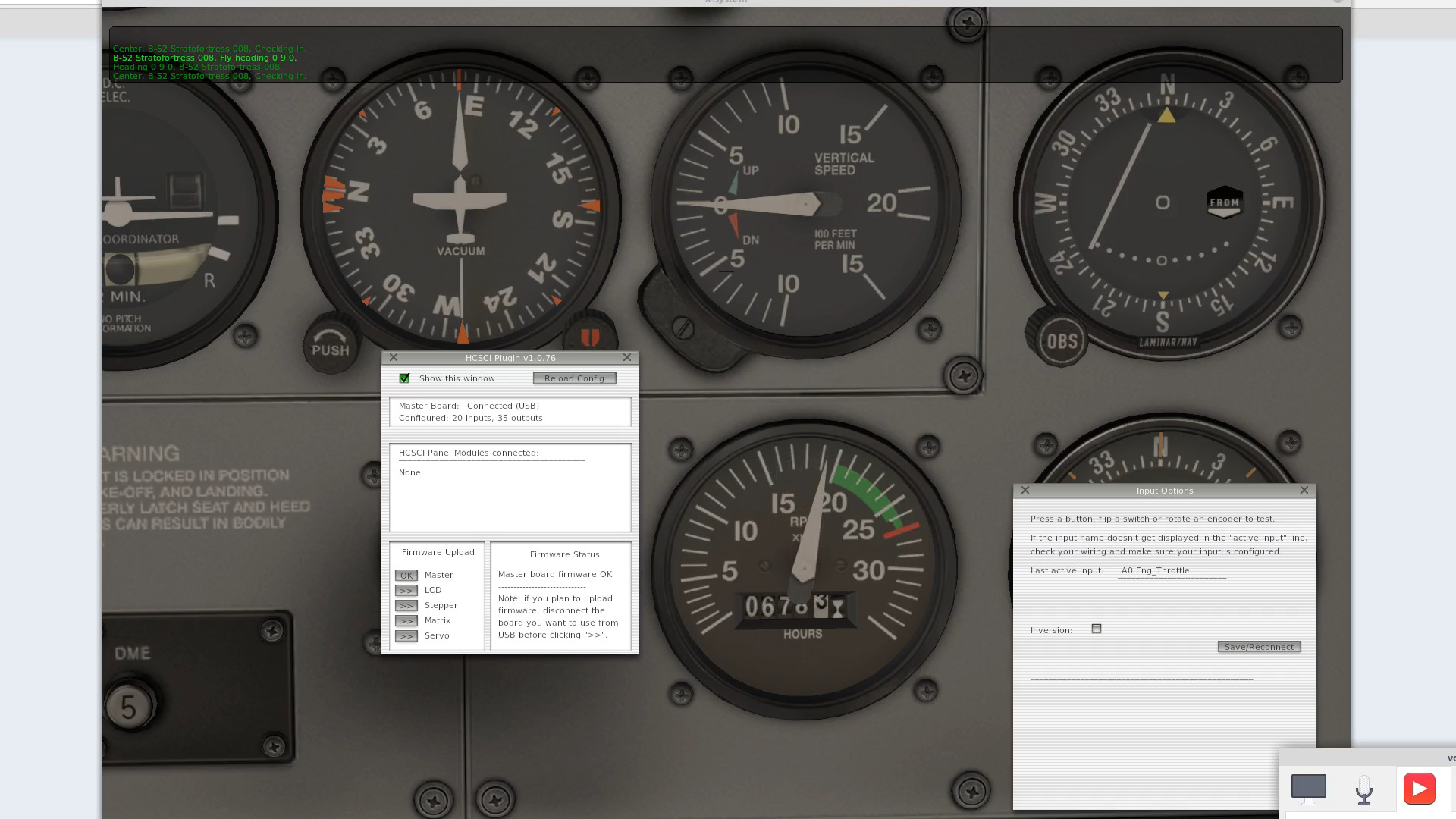
I'm using the same slide potrentiometer ( with linear scale of course) with about 55 mm stroke.
The default precision set is 100 for main control axis and engine controls, but you can try for yourself to adjust it by adding the "p=N" option to the analog input line, where "N" is the number of steps (max=1000). For example: A1 Eng1_Prop_Control p=200
Note, that this default precision for some parameters is set on purpose, to avoid constant fluctuations due to noise being sent to the plugin, which may interfere with the smooth movement of encoders. The highest possible precision is 1000, which will almost certainly result in constant noise, so better try lower values first, like 100-200).
Besides, the separate USB joystick is a HID device with specialized controller, that don't have to process a huge amount of inputs, encoders and doesn't process any input data usually.
Also, no matter what USB joystick you have, is never has real precision more than 300, in most cases it's only 50-100.
Please read my notes here.
-----------------------------
2) Note: for the Prop control (prop pitch lever or constant RPM lever) the plugin reads the aircraft properties on start, such as the ../acf_prop_type, to define what control type HCSCI function to use - either direct/manual pitch prop setting or the handle is used for engine with "constant RPM" prop type (mostly in turboprops).
Can you clarify that prop type in your model is set correctly in PlaneMaker?
Vlad